Méthode MRP : le messie de votre réapprovisionnement de stocks
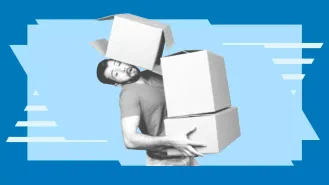
L’organisation de vos ressources de production constitue un enjeu de taille, qui n’est pas évident à cerner et un atout pour la fonction logistique. De combien d’unités avez-vous besoin exactement ? Pour quand devez-vous les programmer ?
Heureusement, toutes ces questions que se posent les gestionnaires ont enfin trouvé une réponse grâce à la méthode MRP. Qu’est-ce que la méthode MRP ? Comment fonctionne le MRP ? On vous explique tout dans cet article !
Qu’est-ce que la méthode MRP ?
La méthode MRP : définition
Le material requirement planning (MRP), ou planification des besoins en composants en français, est une méthode de gestion de la production et des stocks. Elle prévoit le calendrier d’utilisation des produits du stock à partir de données techniques et commerciales.
Pour faire simple, c’est un logiciel qui vous permet de prévoir et de calculer les quantités de matériaux dont vous avez besoin pour votre production. Il vous permet aussi de connaître le moment où vous en aurez besoin, et d'acquérir les quantités achetées ou à réapprovisionner.
Depuis les années 1970, la méthode MRP a connu nombres d’évolutions (MRP II, ERP).
Les types de données de la méthode MRP
Afin que la méthode MRP fonctionne correctement, voici les données d’entrée que vous devez intégrer dans le système :
- La nomenclature. Il s’agit de la liste des matériaux nécessaires afin d’obtenir une unité de produit fini. Elle comporte les matières premières, leur quantité ainsi que les processus de production. L’oubli d’un composant dans l’arborescence du produit fini ou l’introduction d’un faux coefficient dans le fichier des nomenclatures peut fausser les résultats du calcul des besoins nets et peut provoquer des ruptures de stocks voire des retards.
- Le livre d’inventaire. Il précise toutes les informations liées au stock (délais d’attente, commandes annulées, inventaire disponible, etc.). Il est utile lorsque vous désirez savoir quelle matière première est disponible à une date donnée.
- Le plan directeur de production. Il indique le nombre d'articles qui seront produits et sur quelle période.
💡À noter : les données doivent êtres justes et régulièrement modifiées en fonction de l’évolution de la demande. Prenez tout particulièrement garde aux données de planification (stock minimal et maximal, délais, stock de sécurité, etc.).
Il faudra également prendre en compte les données de sortie suivantes :
- Le plan directeur de production recommandé. Il permet de planifier les dates liées au processus de production (début et fin de période), les quantités et la liste du matériel.
- Le programme d'achats recommandé. Il vous renseigne sur les dates exactes de la réception de votre matériel ou la prévision de commandes afin qu’elles soient coordonnées au plan directeur de production.
En bref, le système MRP permet d’acquérir le matériel nécessaire pour maintenir un niveau de stock minimal, afin d’approvisionner le site de production en maintenant une planification efficace des activités de fabrication, d'achat et de livraison du matériel.
Les 4 principales fonctionnalités de la méthode MRP
Calcul des besoins nets
Calculez vos besoins nets en matières premières ou en composants grâce aux données de sortie (programme directeur de production).
Dans un premier temps, la méthode vous permet de calculer les besoins bruts (avec la nomenclature) puis les besoins nets (avec les stocks et les encours).
Calcul des besoins en capacité
En lui associant les différentes gammes d’opérations, vous pouvez calculer les frais de main d'œuvre ainsi que les moyens de production utiles à vos besoins.
Planification à long terme
Présentez les données commerciales (ventes prévues, commandes) et les données techniques (gammes d’opérations, postes à charge) afin d’optimiser les flux de travail, les capacités de production et ainsi atteindre vos objectifs.
🛠Ganacos par exemple, est un logiciel de planification et d’aide à la décision flexible et collaboratif qui vous accompagne au quotidien dans le pilotage de votre processus S&OP. Grâce à des fonctionnalités de gestion logistique intelligentes, des seuils d’alertes personnalisables vous préviennent lorsque le niveau de vos stocks est bas. Ces données sont centralisées et reliées avec vos données commerciales, ce qui vous permet de planifier votre production plus précisément. Le plus ? Vous profitez d’un module de calculs des besoins nets intuitif afin de prendre des décisions plus éclairées.
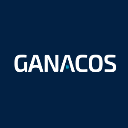
Ganacos
Système d’information
Grâce à son automatisation, vous pouvez gérer les ordres de fabrication ou de commande et piloter la production des produits.
Pour en savoir plus :
Quels sont les avantages de la méthode MRP ?
La disponibilité de la matière première
En adoptant la méthode MRP, vous pouvez avoir connaissance de la quantité de matières premières disponibles en amont et ainsi organiser de façon plus efficace le management de vos projets de production et de vos ressources.
Le respect des délais de livraison
En coordonnant vos équipes et en prenant connaissance de la situation de votre gestion de production, vous êtes plus à même de prendre des décisions pertinentes, mais surtout remplir les délais demandés.
Respecter les délais sur le long terme est la promesse d’une amélioration de votre satisfaction client ainsi que de votre image de marque.
Le maintien d'un faible niveau de stock
Évidemment, vous êtes libre de choisir votre propre quantité de commandes économiques ou le niveau de stock que vous jugez optimal tant que vous répondez à la demande et que vous évitez des coûts de stockage trop élevés ou du gaspillage de matériel.
En gardant des stocks faibles, vous pouvez garantir suffisamment de matériaux pour poursuivre la production tout en faisant des économies. La méthode MRP vous permet justement de maintenir un niveau de stock suffisamment faible et d’éviter des pertes.
La planification des activités de fabrication
Prenez connaissance en temps réel de vos activités de fabrication à la façon d’un tableau de bord logistique. En suivant les différentes étapes, vous pouvez organiser de manière optimale vos activités logistiques. En fonction des délais et des priorités, les dates de début des opérations affichées sur le logiciel, vous pouvez organiser votre charge de travail et ainsi remplir vos objectifs.
La réduction des coûts
Sur le long terme, il est fort probable qu’un cercle vertueux prenne forme et entraîne la réduction de vos frais (surcoût de stockage, réduction des coûts logistiques de fabrication, réduction des stocks, limitation du gaspillage…).
En effet, si vous gérez d’une main de fer vos stocks de matières premières et vos délais de livraison, il est évident que vous obtiendrez non seulement de meilleurs rendements, mais aussi une baisse significative de vos coûts.
Quels sont les inconvénients de la méthode MRP ?
Nécessite une main d’œuvre suffisamment qualifiée
Vu le caractère assez technique de la méthode MRP, qui consiste à traiter des données et des indicateurs spécifiques, vous ne pouvez pas le faire faire par n’importe qui.
Un conseil : désignez un expert parmi vos équipes qui sache parfaitement utiliser cette méthode afin d’en faire un résumé compréhensible à vos différents agents.
S'adapte peu aux produits trop personnalisés
Le MRP est un système complexe qui fonctionne mieux pour des nomenclatures stables. En effet, le calcul des besoins ne se fait pas seulement sur la base de la nomenclature de références finales. Ainsi, cela demanderait de reproduire une nouvelle nomenclature pour chaque demande faite sur mesure.
Et vous, utilisez-vous la méthode MRP ? Êtes-vous satisfaits ? Quels sont vos conseils pour optimiser votre production et vos stocks ? Dites-nous cela en commentaires !